Choosing the Right Commercial Door: Top 5 Considerations
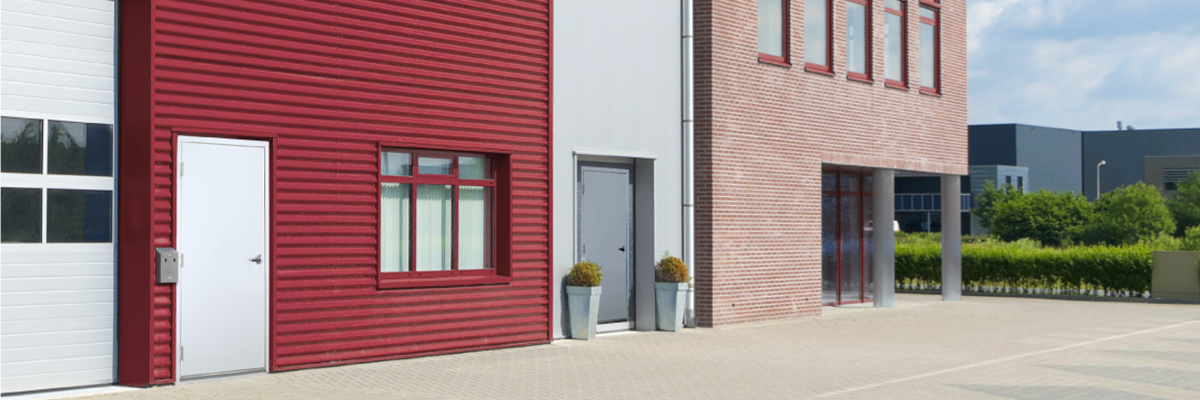
Make It Memorable, Meet the Codes, Maximize Functionality
When you are walking through an office building, the local mall, or a doctor’s office, you may take notice of the large glass display at the building’s entryway, or the polished metal of the door handle as you open it. These doors are engineered to provide a glimpse of what is to unfold inside and are part of the initial statement a building will make to passersby, visitors, and occupants. The multitude of considerations that went into selecting that door poses a challenge for architects, designers, and building owners who must balance utility and security with aesthetics. Together, those stakeholders must ensure that the intended architectural design of the building comes to life – from the doors that serve as the entrance to the doors on the inside – while also considering a host of other functional mandates.
Beyond the aesthetic impact a door will deliver, designers and architects must ask a series of critical questions when they begin selecting the doors for a project:
- What is the right size and configuration for the door?
- Are there any logistical challenges as it relates to installation or maintenance?
- What building codes impact the selection of the doors on the project?
- How can the doors contribute to a productive space for occupants?
From architectural trends to technology advances and changing societal needs, the design of today’s commercial buildings has evolved, all aimed at improving the way we interact with buildings and spaces. The doors specified for those buildings play a pivotal role in this equation.
Here are five questions to pose when specifying and selecting the right doors for the next project on your list.
What Kind of Wall?
Whether replacing a door on an existing structure or specifying doors for a new building, the first consideration is the type of wall that will surround the door. Each wall type comes with different installation techniques.
Take a cinderblock or masonry wall. Generally, the frame will need anchored into the concrete by expansion bolts, or the wall would need to be built around the frame with masonry anchors or wire anchors. In this case, the frame is generally welded, meaning the frame is essentially preassembled in a singular piece.
In comparison, if you take a drywall wall, frames are typically shipped in a knock down state, meaning you have separate pieces to install. Knocked down door frames typically come in three pieces: hinge, strike, and header jamb components. With drywall applications, the wall thickness becomes more critical. The frame for the door will then slide over an existing drywall opening wall, as these types of door frames are mounted and installed differently.
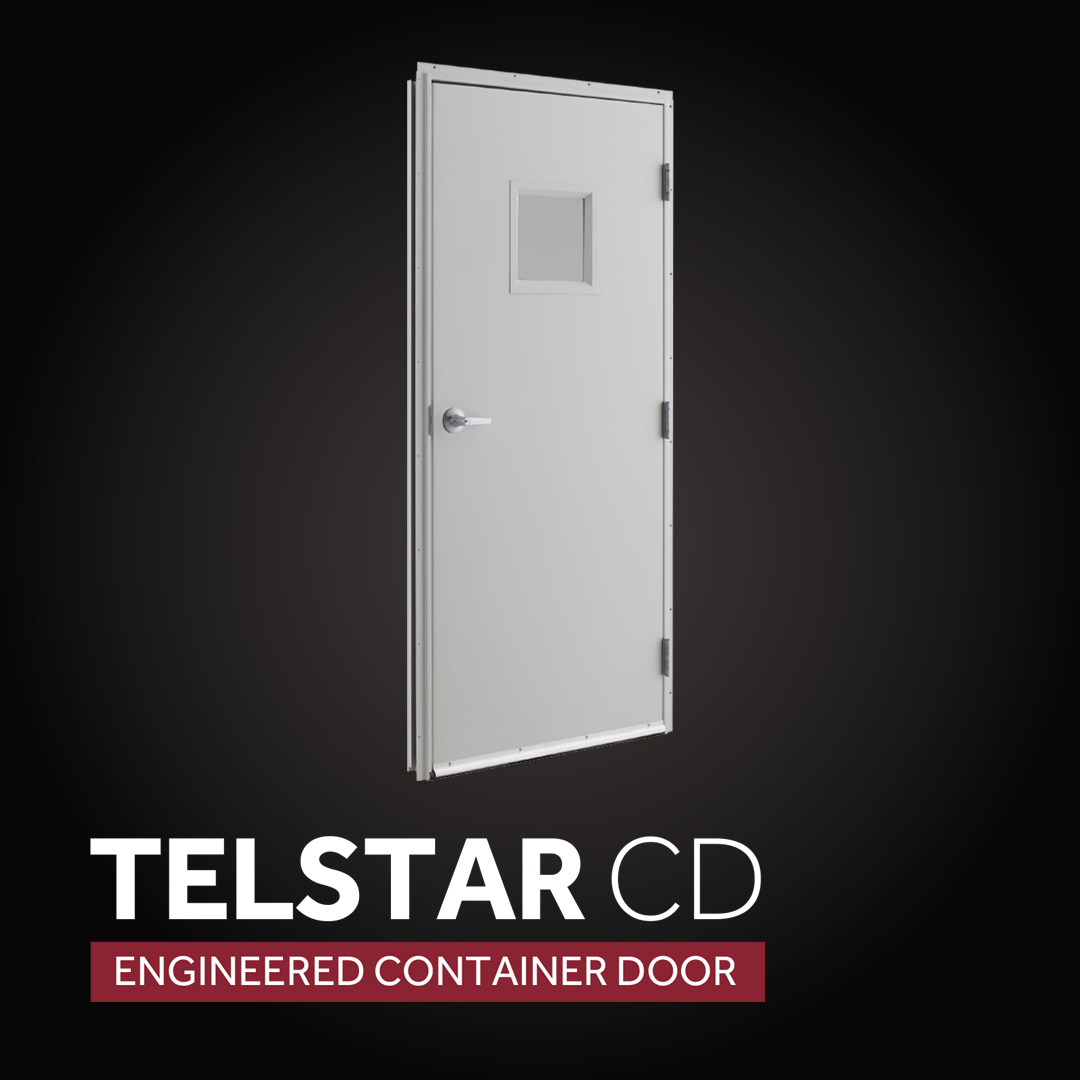
What Kind of Door?
Once the wall assembly is confirmed, it is time to choose the door type. What is the best material to choose? Should it be a metal door, or should it be made of wood? Should it consist of composite material? Where is the door located on the building – on the exterior, or in the interior of the structure?
How the door will be used – and where it will be located – are critical considerations for choosing door materials. For instance, some exterior entrances may be better suited for an insulated door, which prevents condensation from forming on the inside of the door and can provide a certain level of sound attenuation. These doors are traditionally hollow metal doors made from galvannealed steel to reduce rust and corrosion properties. Within the hollow metal door is an insulated foam core, often comprised of polystyrene. With a polystyrene core, the doors deliver higher R-values and U-values and provide superior thermal performance and durability.
Hollow metal doors by Tell Manufacturing are designed to fit nearly any wall and entry requirement, with superior strength and durability for institutional, commercial, and industrial applications. Made from galvannealed steel and a polystyrene core, Tell hollow metal doors are fire rated up to three hours.
How Should It Swing?
The importance of door handing plays a large role in the functionality of the space. Door handing refers to the way the door is designed to swing. A right-handed option means that when standing outside the door, the hinges are on the right side, making the door swing inward. A right-hand reverse door means the hinges are still on the right side, however the door would now swing outward. Door swing is a key factor in maximizing functionality and convenience of a space for each application.
Locations of hinges and locks on a door can vary, depending on the manufacturer’s specifications. This comes into consideration when you have a door frame that is still in good condition, but you are looking to replace a door with heavy rusting. This is common in replacement doors where facilities are aiming to keep consistency among doors. The height of the door comes into consideration as well. An 8-foot door has four hinges, and a 6-foot door only has three hinges.
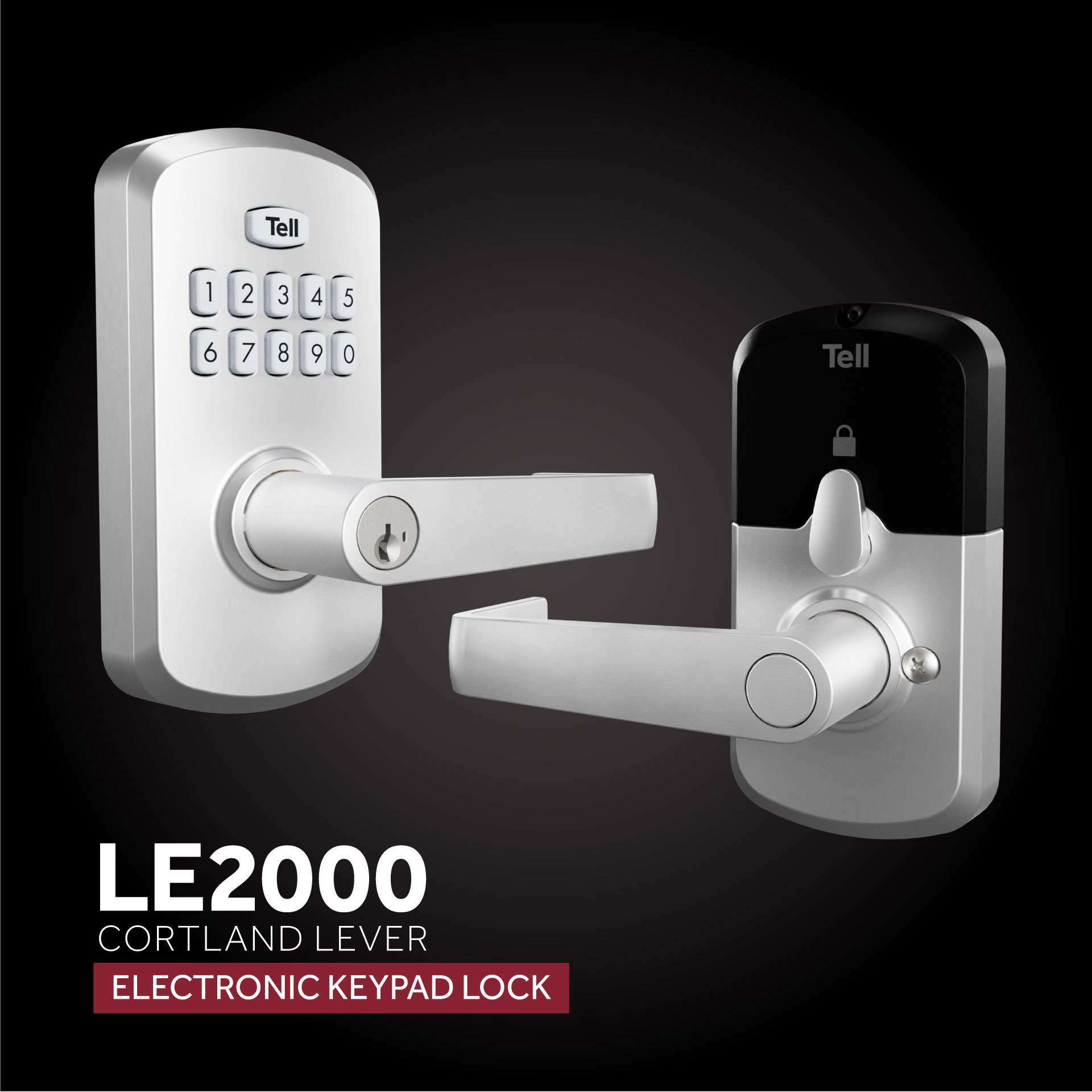
What Hardware is Necessary?
Prepare the door to ensure that locks and accessories fit into the door seamlessly. Do you want a deadbolt lock, or do you want a lock with a lever? For proper installation, drill holes to match the template measurements of desired hardware selections and any additional attachments or accessories.
With different doors come the option for different locksets. The standard mockup includes 161 Lock Prep, which is designed for cylindrical lock installation. Buildings with higher security requirements such as government facilities, hospitals, or universities may specify a mortise lock to meet specifications. Mortise locks are larger in size and include several components, including the lock body, latch bolt, strike plate, key cylinder, faceplate, and more. These locks require a mortise lock prep, also known as an 86 prep. Also, ensure that any ramps, step-ups, strikes, or reinforcement points are specified and measured accurately for proper installation and functionality of the door.
Is the Door Code Compliant?
Regardless of the environment, prioritizing a building's adherence to code compliance, fire safety standards, and emergency egress is crucial when choosing and installing commercial doors.
Depending on building codes, fire-rated doors may be required based on occupancy type, size and use. Different doors throughout the building may require fire ratings ranging from 20 minutes to three hours. Fire-rated doors are meticulously crafted using materials that resist flames, smoke, and heat transfer. These doors are commonly made with a combination of materials including steel, metal, aluminum and fire-rated glass.
In many circumstances, commercial doors, along with the hardware, are required to be compliant with the American Disabilities Act (ADA). In particular, entryways that have public means of egress must be complaint with ADA regulations. Door widths, thresholds, and doorways must also meet certain criteria. For instance, for a door that has a full lite piece of glass, the glass cannot be lower than 10 inches above finished floor so that wheelchair accessibility is safe and functional.
In a similar case, consider the scenario of approaching a stairwell door when you may be unsure if someone is on the other side. Those doors often have a narrow glass slit in the door, which is required to be 43 inches above the finished floor.
Door hardware must also be compliant when it comes to ease of operation. Designers must ensure that doors they specify have levers instead of knobs so that the handles are accessible to all. Door closers must also meet the pounds per foot requirement, ensuring that doors are able to be pushed open with ease in the event of an emergency.
Back to the Basics: Simplifying Selection
Choosing the right door for your commercial space requires solving a complex equation that must consider a variety of factors: design elements, code compliance, installation, logistics, safety, and budget.
Jumpstart the specification process by asking three basic questions:
- What kind of wall am I working with?
- How do I see the door performing?
- Who will be using the door, and what access do they need?
Answers to these questions can go a long way toward choosing the optimal solution that will serve the building and its occupants for years to come.